Injection Moulding Manufacturing: Empowering the Future of Custom Parts Production
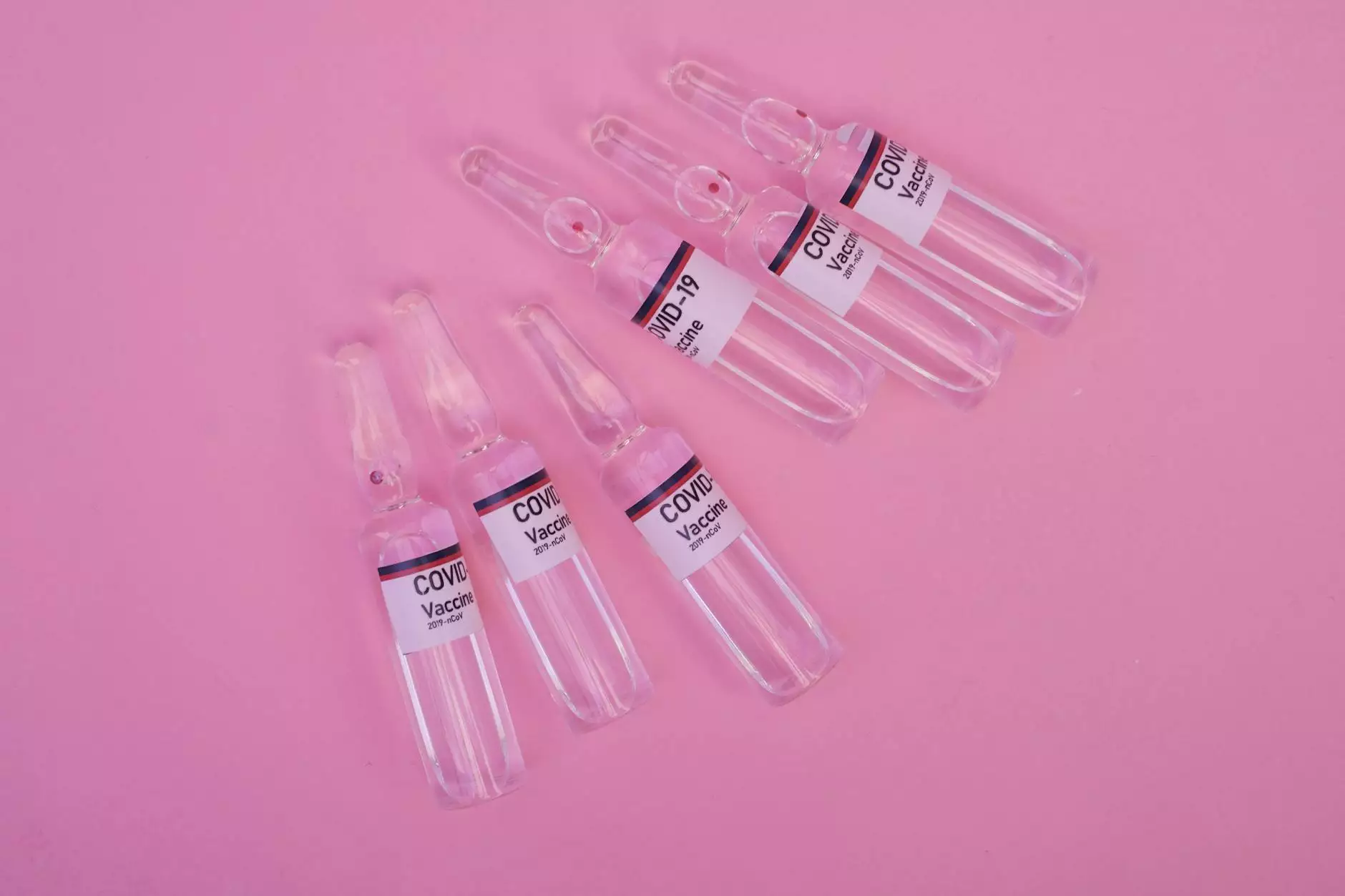
Injection moulding manufacturing is a cutting-edge process that has revolutionized the production of plastic parts across various industries. This article will provide a comprehensive overview of injection moulding, examining its benefits, applications, processes, and the future of this manufacturing technique. Whether you are an engineer, a business owner, or simply someone interested in manufacturing technologies, this guide will offer valuable insights into how injection moulding can enhance production capabilities.
Understanding Injection Moulding Manufacturing
Injection moulding is a manufacturing process for producing parts by injecting molten material into a mould. The process is predominantly used for plastics, but can also be adapted for metals and ceramics. This technique is favored for its ability to produce complex shapes, high precision, and the efficiency with which it can produce high volumes of parts.
The Injection Moulding Process
The injection moulding process involves several key steps:
- Material Selection: The choice of material is vital, as it impacts the quality and characteristics of the final product. Common materials include thermoplastics such as ABS, polycarbonate, and polypropylene.
- Mould Design: Designing the mould is a critical step that requires precision to ensure that the final product meets specifications. The mould often includes intricate features to create the desired shapes.
- Melting the Material: The selected material is heated to a molten state, in a machine known as an injection moulding machine.
- Injection: The molten material is injected into the mould under pressure. This is where the part begins to take its shape.
- Cooling: The material cools and solidifies in the mould, allowing it to take the final desired shape.
- Demoulding: Once cooled, the mould opens, and the finished part is ejected.
- Finishing: After the part is demoulded, it may require additional processing to achieve the desired finish.
Advantages of Injection Moulding Manufacturing
The injection moulding process offers numerous advantages, making it a preferred choice among manufacturers:
- High Efficiency: Once the moulds are created, the production process can run continuously, producing thousands of identical parts quickly.
- Consistency and Precision: The process ensures high accuracy and repeatability, which is essential for industries that demand tight tolerances.
- Material Versatility: A wide range of materials can be used, including engineered plastics that have enhanced properties.
- Complex Geometries: Injection moulding can create intricate designs that would be difficult or impossible to achieve using other methods.
- Reduced Waste: The process produces minimal scrap material, making it a more sustainable option compared to other manufacturing techniques.
Applications of Injection Moulding Manufacturing
Injection moulding manufacturing has a broad spectrum of applications across various industries:
Automotive Industry
The automotive sector utilizes injection moulded parts for a range of applications, including:
- Dashboard components
- Exterior trim pieces
- Various interior parts
By using injection moulding, auto manufacturers can reduce weight and costs while improving strength and design flexibility.
Consumer Electronics
In the realm of consumer electronics, products such as smartphones and laptops often include injection moulded components. These parts are crucial for:
- Enclosures
- Buttons and switches
- Connectors
A focus on aesthetics and ergonomics drives the design of these components, with injection moulding meeting high-quality standards.
Medical Devices
The medical industry relies on injection moulding for producing precise and sterile parts used in devices, instruments, and packaging. Notable applications include:
- Syringes
- Implants
- Diagnostic tools
Due to the strict regulations in this field, injection moulding ensures the required quality control and product integrity.
The Future of Injection Moulding Manufacturing
As technology continues to advance, the injection moulding sector is witnessing several trends that shape its future:
Automation and Industry 4.0
The incorporation of automation and smart technology within injection moulding processes is streamlining operations. This includes:
- Real-time monitoring of production conditions
- Predictive maintenance of machinery to minimize downtime
- Integration with supply chain systems for efficient inventory management
Advancements in Materials
Research and development are constantly improving available materials, leading to enhanced properties such as:
- Increased strength-to-weight ratios
- Improved temperature resistance
- Eco-friendly bioplastics that reduce environmental impact
3D Printing and Injection Moulding
The marriage of 3D printing and injection moulding is creating new avenues for prototyping and low-volume production. This combination enables:
- Faster turnaround times for prototype development
- Increased flexibility in design changes
- Cost-effective solutions for small batch productions
Partnering with Experts in Injection Moulding Manufacturing
Choosing the right partner for your injection moulding manufacturing needs is crucial for your business success. Here at Deep Mould, we specialize in providing high-quality injection moulded components tailored to your specifications. Our expertise encompasses:
- Custom Mould Design: We leverage advanced design techniques to create bespoke moulds that meet your exact requirements.
- Material Consultation: Our team can advise on the best materials suited for your project, optimizing performance and cost.
- Quality Assurance: We adhere to strict quality control standards at every stage of production, ensuring that our products are reliable and durable.
Conclusion
In conclusion, injection moulding manufacturing is a vital technology that plays an essential role in modern production across various sectors. Its advantages in efficiency, precision, and sustainability make it a prime choice for manufacturers looking to innovate and scale their operations. As we move into an era of advanced manufacturing technologies, injection moulding will undoubtedly continue to evolve, offering exciting opportunities for businesses worldwide. By partnering with Deep Mould, you can leverage our expertise to unlock the benefits of injection moulding for your next project.
For more information about how our solutions can transform your production process, visit us at Deep Mould.